How to Conduct a Pressure Test on Industrial Valves: A Step-by-Step Guide
- unisonvalves
- 5 days ago
- 5 min read
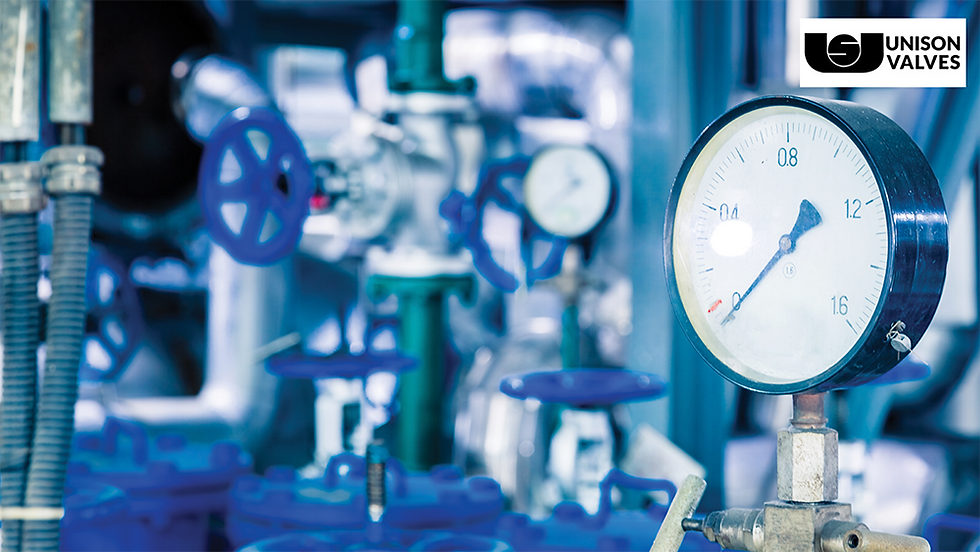
In industries like oil, gas, power, water treatment, and chemical processing, the integrity of every component plays a critical role in ensuring safe and uninterrupted operations. Industrial valve testing is a pillar of reliability, helping avoid costly failures, unplanned shutdowns, and safety hazards.
Unison Valves, a trusted valve manufacturer in Maharashtra, has been at the forefront of providing top-notch industrial flow control solutions. Pressure testing forms a core part of their commitment to safety, quality, and operational excellence.
Let’s explore the step-by-step valve testing guide to understand how pressure tests help ensure leak-proof valves for industries, drive predictive maintenance, and enhance overall equipment reliability.
Why Industrial Valve Testing is Critical
Why is industrial valve testing essential for safe operations? Because when valves fail, systems fail.
Whether in power plant valve testing, chemical industry valve testing, or oil and gas valve pressure testing, the goal remains the same: to prevent leakage, maintain consistent pressure, and ensure smooth flow control.
Modern-day systems also rely on smart valve solutions for better monitoring and predictive maintenance valves which reduces downtime. From HVAC applications to complex chemical plants, industries are turning to tested valves to ensure long-term safety and efficiency.
Types of Valves Commonly Pressure Tested
Understanding the valve type is the first step in pressure testing.
Popular variants include:
Ball valves (especially by ball valve manufacturers in India) are known for their simple operation and durability.
Gate valves made by gate valve manufacturers in Pune are ideal for on/off control.
Globe valves from globe valve manufacturers in Pune, excellent for throttling.
Lift check valves are designed by lift check valve manufacturers to prevent backflow.
Butterfly valves for HVAC and water treatment, including options from leading manufacturers of lever & gear-operated butterfly valves in India.
Each type has unique pressure testing needs depending on its design, usage, and fluid type.
Pressure Testing Methods: Hydrostatic vs. Pneumatic
What’s the difference between hydrostatic testing valves and pneumatic testing for industrial valves? Both methods serve different purposes.
Hydrostatic testing valves involves using water to pressurize the valve and check for leaks or structural weaknesses.
Pneumatic testing for valves, on the other hand, uses air or inert gas, making it suitable for delicate valves or systems that cannot be exposed to water.
Here’s a quick breakdown:
Hydrostatic testing step-by-step:
Fill the valve with water
Apply test pressure
Inspect for leaks, bulges, or pressure drops
Pneumatic testing for safety:
Use only in well-ventilated, controlled environments
Follow strict safety protocols due to the compressibility of gases
Use hydrostatic testing for industrial valves in general applications and pneumatic testing when moisture is a concern.
Step-by-Step Valve Pressure Testing Guide
Pre-Test Preparations
Start with valve inspection and testing preparation:
Visual inspection for defects
Document valve specifications and test standards
Set up the valve on the test bench
This is where the foundation of a safe test lies.
Applying Pressure as per Standards
Follow updated 2025 pressure test protocols for industries such as pharmaceuticals and chemicals.
Use calibrated equipment
Adhere to required pressure levels for a specified time
Reference relevant step-by-step testing instructions from international standards
Test Execution: Monitoring for Leaks & Deformation
During the test, look for:
Pressure drops on gauges
Bubble formation or physical deformation
Alerts from digital sensors and leak detectors
Leakage compromises the entire system. Leak detection valves and ensuring leak-proof valves for industries are key.
Post-Test Analysis & Certification
After the test:
Analyze data from sensors and inspection logs
If required, perform a retest or corrective maintenance
Issue compliance certification as per the valve inspection and testing guide
This phase ensures that only the safest valves reach your systems.
Ensuring Industrial Safety & Reliability
How does pressure testing ensure safety in critical systems? By acting as the first line of defense against failure.
Industries such as oil & gas, chemical processing, and fire safety systems depend on flawless valve operation. Oil, gas, and chemical valve testing prevents incidents, protects assets, and supports environmental safety.
Adopting best practices for industrial valve testing and regular inspection enhances system dependability and compliance. At Unison Valves, we conduct pressure testing according to valve classes ranging from #150 to #800. We take pride in ensuring that each valve undergoes rigorous testing to meet international standards. Only after the valve successfully passes these tests do we proceed with final dispatch, ensuring that each product meets the highest level of safety and operational reliability.
Valve Manufacturers and Suppliers in India
Choosing the right manufacturer impacts testing quality and product durability.
Unison Valves, a reputed valve manufacturer & supplier in Pune, has consistently delivered high-quality, tested products. Whether you're in Mumbai, Pune, or cities like Aurangabad, Nagpur, Unison ensures you receive dependable service.
Expanding across Bangalore, Chennai, Hyderabad, Telangana, Andhra Pradesh, and Tamil Nadu, Unison is among the top industrial valve manufacturers in Mumbai and Pune. As valve supplier companies in Aurangabad and other regions, they uphold rigorous standards.
Whether you need ball valve manufacturers in India or are exploring the top valve manufacturing companies in Pune, trust Unison Valves.
Advanced Technologies in Valve Testing
Modern valve testing is evolving with tech.
Use of automatic ball valves for remote and consistent operation
Integration of the Valve position indicator limit switch box for real-time feedback
Smart diagnostics through IIoT for live condition monitoring
These innovations allow industries to shift from reactive to predictive maintenance and improve operational uptime.
Final Thoughts
Valve pressure testing is more than a quality check—it’s a commitment to safety, efficiency, and system longevity. By following the right pressure test procedure explained above, industries can confidently rely on their valve infrastructure.
Choose reliable partners like Unison Valves, where quality, innovation, and trust flow together. From Pune to Pan India, they are redefining standards in the valve manufacturing space.
Frequently Asked Questions (FAQs)
How to conduct a valve pressure test?
Ans- Follow the step-by-step valve testing guide: Inspect, set up, apply pressure, monitor, and analyze results.
What is the difference between hydrostatic and pneumatic testing?
Ans- Hydrostatic testing uses water and is safer for most valves. Pneumatic testing uses gas and requires more safety precautions.
Which valves are suitable for the oil and gas industry?
Ans- Ball valves, gate valves, and globe valves are commonly used for their pressure-handling capacity and durability.
What are the safety standards for valve pressure testing in 2025?
Ans- Adherence to updated protocols, calibration of test equipment, and certified inspection processes are key requirements.
Where can I find reliable valve manufacturers in India?
Ans- Unison Valves is a leading valves manufacturer & supplier in India, with a strong presence across Maharashtra and southern India.
Comments